Hydraulic Repairs
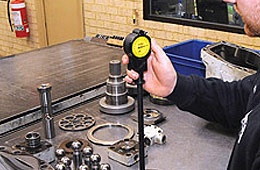
Dismantle & Assessment
• On arrival all components are documented, cleaned and completely dismantled
• All wearing parts are precisely measured and the result recorded
• Hydraulic components that have excessive or unusual wear are subject to further review
• The results of the inspection procedures are then used to develop an effective scope of work
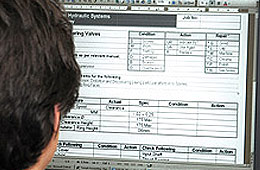
Quoting & Procurement
• Internally developed, Quality Assured disassembly and inspection sheets are utilised to provide efficient and accurate information transfer between the technical and administrative staff
• An extensive inventory is maintained, ensuring fast turnaround and reducing reliance on secondary suppliers
• HYCON has access to genuine parts for the world’s leading brands through a diverse international supply chain

Grinding
• All surface grinding is completed in-house to maintain quality standards
• A larger diameter wheel is used to ensure superior finish
• This grinder is supported by a large range of jigs and fixtures to facilitate rapid turnaround
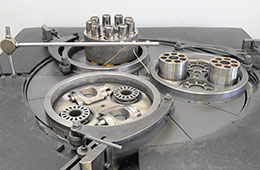
Lapping
• HYCON has extensive internal lapping capabilities with five lapping machines
• Where external Lapping Services are required, HYCON engages a specialised provider
• The lapping room tables are audited daily to maintain accuracy
• Both flat and spherical components are catered for
• Optical flats, in conjunction with monochromatic light, are used to check flatness lapping
• All lapped components are ultrasonically cleaned to remove any residue
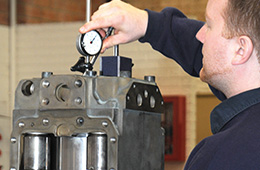
Assembly
• All components are reassembled by skilled technicians with years of experience using Quality Assured processes
• All critical dimensions are counter checked, with measuring equipment that is calibrated monthly
• All critical specifications, assembly dimensions and tensioning requirements are recorded for quality assurance and future reference
• Overhead cranes with creep mode hoists enable the precision assembly of large and heavy components
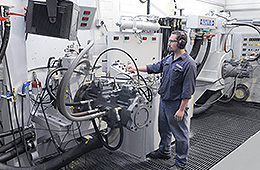
Testing
• All hydraulic components are subject to an exhaustive and authentic function test using a facility unrivalled in Australia
• Four test stands are available (110,250,300 and 1000 kW), and these can be run simultaneously
• The largest pumps can be tested at full displacement and design pressures, at the correct speeds
• All tests are logged and analysed using Hydrotechnik 5070, 8050MC hardware and software with VSE flowmeters
• Special care is taken to protect components when testing, oil flow is full flow filtered to 10 micron and off line filtered to 3 micron
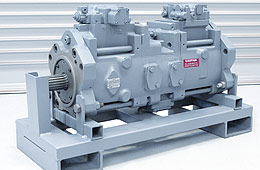
Sealing & Packing
• Ports on repaired components are sealed with steel blanks at the completion of testing, preventing ingress of contaminants and loss of oil during transportation and storage
• Unpainted machine faces are coated to prevent corrosion
• All components can be packaged and transported per customer requirements. Hycon can offer the following Options:-
- Metal Transport Box
- Wooden Crates
- Anti Corrosion film covering on skid
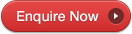